From mid-century modern to 3D plywood
One of the most important factors in the epoch-making breakthroughs and turning points of pressure-treated plywood was the development of adhesives. The Estonian company Lutherma was able to be the market leader in this field before World War I because they developed a waterproof adhesive, and the Eames couple—Charles (1907-1978) and Ray Eames (1912-1988)—were then able to have a bi-directional bending profile for the first time (creating a real space shape that is well resistant to both forces and loads in different directions, eliminating previous stability-stiffness problems) when they obtained an adhesive developed for war purposes.
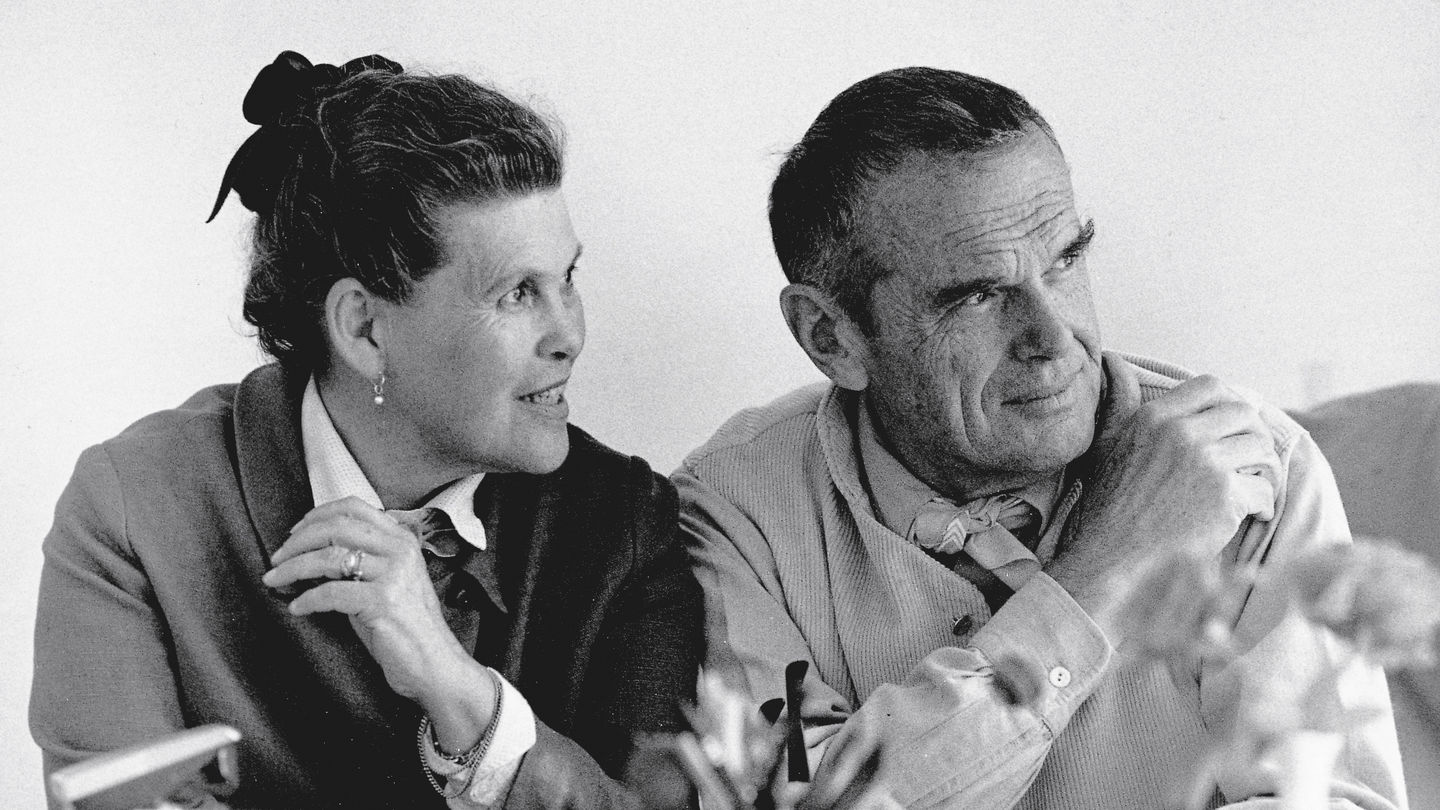
In this era (mid-20th century, mid-century modern), which can also be called the classic, mature era of plywood, the manufacturing technology of the material still known and used today was created. The importance of ergonomics was also strengthened in the war, as more than four hundred flight incidents occurred due to incorrect identification of controls, that is poor ergonomic design—this practical knowledge still plays a significant role in the development of seating.
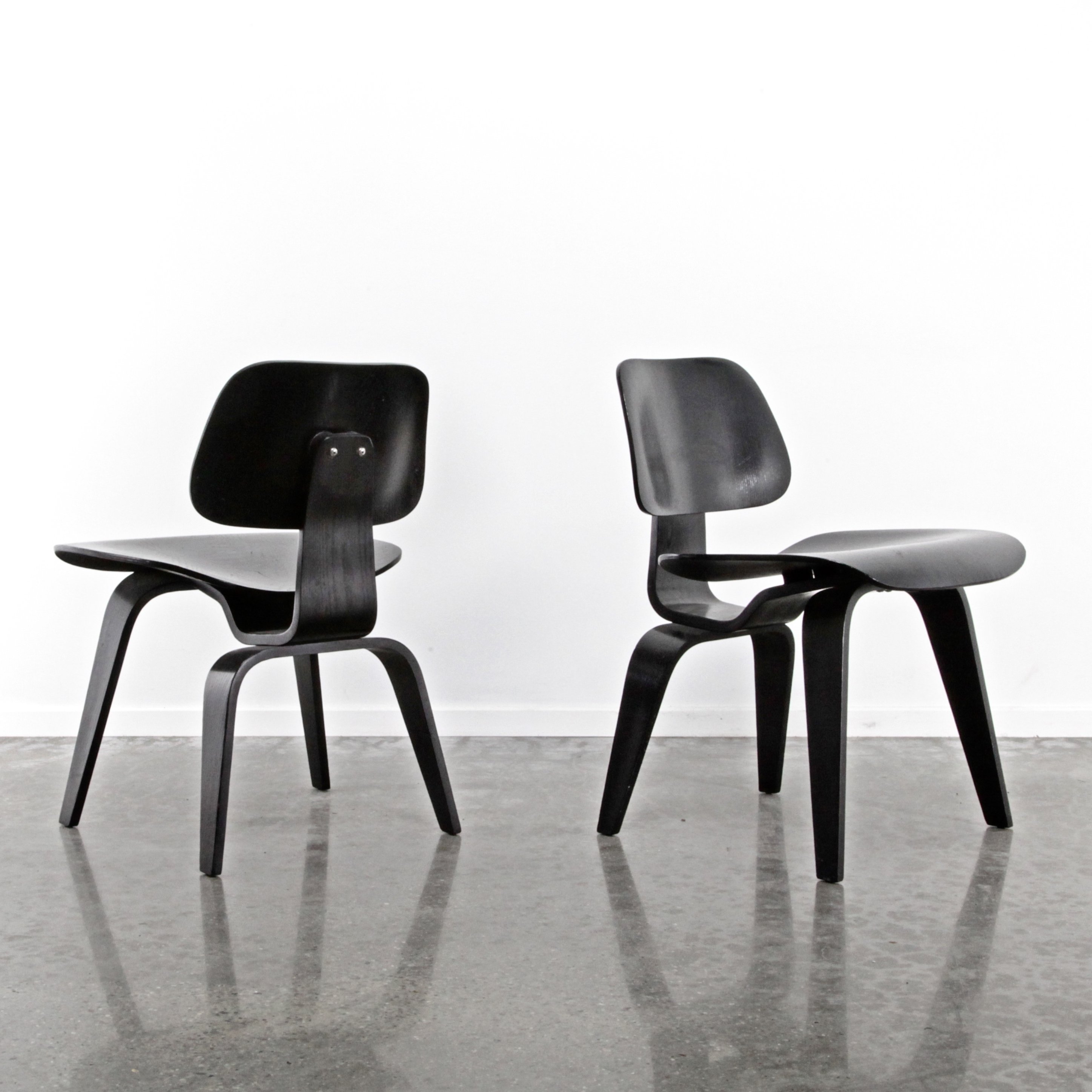
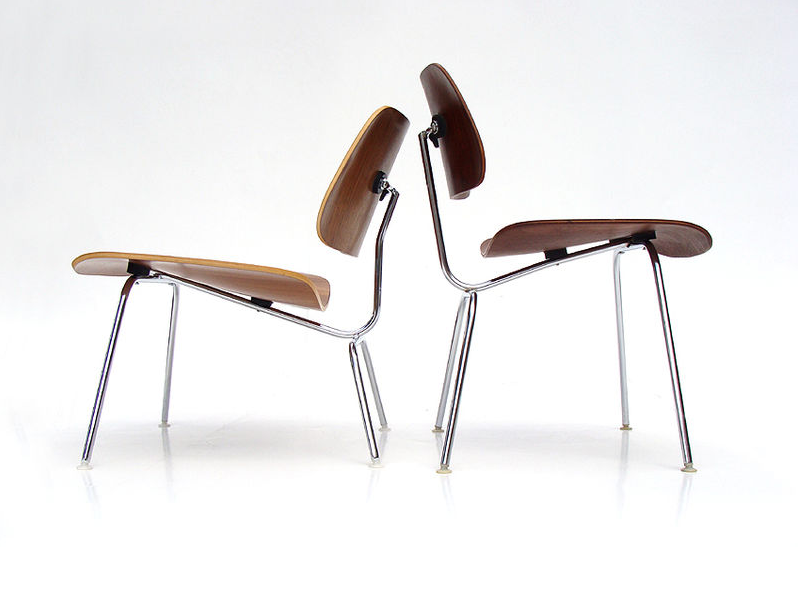
Developments in the 21st century significantly expand the possibilities of using plywood and go beyond the old limits. The German company Reholz (now Danzer) has developed the 3D plywood technology, which allows the formation of organic shapes while preserving the ease of shape preparation, but without reducing the load-bearing capacity and stability. This technology gives the design freedom that designers experimenting with plywood have always longed for—this is perhaps most spectacularly achieved in the structure of the eggshell. This is because the seemingly fragile and thin eggshell can withstand a relatively large load without breaking. 3D plywood allows the production of similarly thin shell structures that can successfully withstand forces from different directions. The only drawback is the high production cost, which was moderated by András Kerékgyártó, lead designer of Plydesign, at the iF Design Award 2021 award-winning FRIGATE chair back, combining the traditional and 3D plywood process.
.jpg)
Nowadays, there is a tendency for companies that have so far used expensive 3D plywood technology to make their products to switch to using cheaper plastic. The “Grada” developed by the Finnish UPM is a process in which plywood, in this case a thermoformable wood board, is heated, then molded and cooled (cold press). This technology significantly shortens the total working time compared to conventional pressure-treatment. They impregnate plywood with Pagholz synthetic resin, which is heat-treated under high pressure—so the material can be bent in small curves and, if necessary, can be formed in three dimensions.
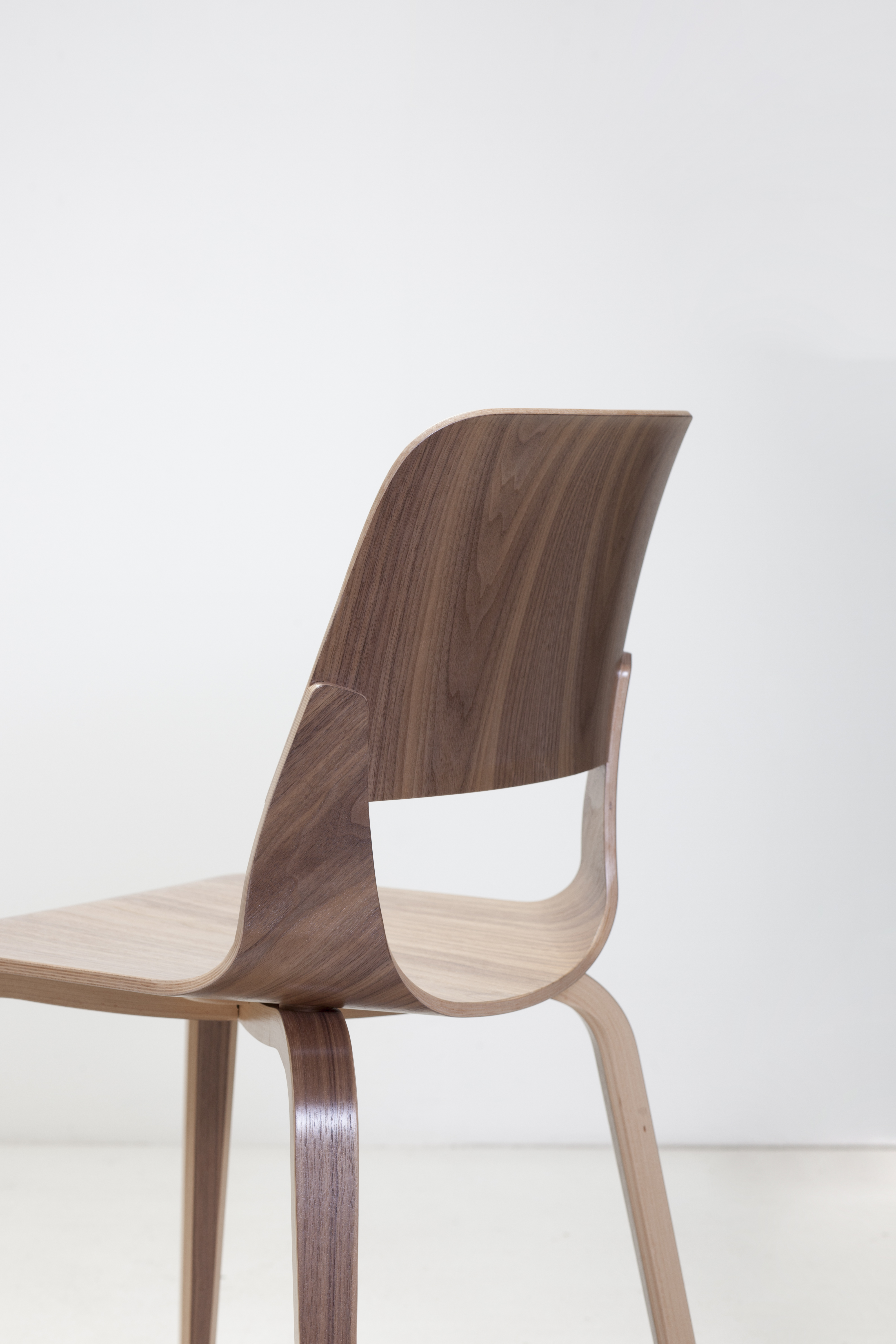
Moreover, according to the latest news, plywood has already conquered space: the Finns will launch their satellite built of birch plywood this year. This is exactly the purpose of the PLY DESIGN HOUSE 2021 open call—to find a new, innovative field of application for plywood, this versatile material. Concepts can be submitted for the application until July 31, further details can be found on the website of the call.